Hardware manufacturers in china introduce you: Grinding wheels, also known as consolidated abrasives, are bonded with ordinary abrasives into a certain shape (mostly circular, with a through hole in the center) and have a certain strength Solidified abrasives. It is generally composed of abrasives, binders and pores. These three parts are often referred to as the three elements of a consolidated abrasive. According to the different classifications of bonding agents, there are ceramic (bonding agent) grinding wheels, resin (binding agent) grinding wheels, and rubber (binding agent) grinding wheels. Grinding wheel is the largest and most widely used type of abrasive tools. It rotates at high speed during use. It can rough, semi-refined, and semi-finely grind the outer circle, inner circle, flat surface and various profiles of metal or non-metal workpieces. Fine grinding and grooving and cutting. The characteristics of the grinding wheel are mainly determined by factors such as abrasive, particle size, bonding agent, hardness, structure, shape and size.
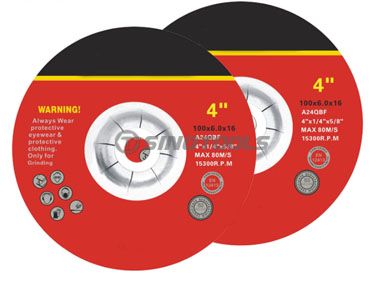
Grinding Wheel
1 Overview
Grinding wheel is the most important type of abrasive tool in the grinding process. Grinding wheel is a porous body made by adding a binder to the abrasive, compacting, drying and baking. Due to the different abrasives, bonding agents and manufacturing processes, the characteristics of the grinding wheel are very different, so it has an important impact on the grinding process quality, productivity and economy. The characteristics of the grinding wheel are mainly determined by factors such as abrasive, particle size, bonding agent, hardness, structure, shape and size.
2 categories
There are many types of grinding wheels. According to the abrasive used, it can be divided into ordinary abrasives (corundum and silicon carbide, etc.) grinding wheels and natural abrasive superhard abrasives and (diamond and cubic boron nitride, etc.) grinding wheels;
According to the shape, it can be divided into flat grinding wheel, beveled grinding wheel, cylindrical grinding wheel, cup-shaped grinding wheel, dish-shaped grinding wheel, etc. According to the bonding agent, it can be divided into ceramic grinding wheel, resin grinding wheel, rubber grinding wheel, metal grinding wheel and so on. The characteristic parameters of the grinding wheel mainly include abrasive, viscosity, hardness, bonding agent, shape, size and so on.
Because the grinding wheel usually works at high speed, a rotation test (to ensure that the grinding wheel does not break at the highest working speed) and a static balance test (to prevent machine vibration during work) should be performed before use. After a period of work, the wheel should be trimmed to restore the grinding performance and correct geometry.
3 attributes
Grinding wheels are circular solidified abrasive tools with through holes in the center made of abrasives and bonding agents.
The characteristics of the grinding wheel are determined by factors such as abrasive, particle size, hardness, bonding agent, shape and size.
4 choice of abrasive
Abrasive is the main raw material for manufacturing grinding wheels, and it is responsible for cutting work. Therefore, the abrasive must be sharp and possess high hardness, good heat resistance and certain toughness.
5 hardness and its selection
The hardness of the grinding wheel refers to how easily the abrasive particles on the surface of the grinding wheel fall off under the action of the grinding force. The hardness of the grinding wheel is soft, which means that the abrasive particles of the grinding wheel are easy to fall off, and the hardness of the grinding wheel is hard, which means that the abrasive particles are more difficult to fall off. The hardness of the grinding wheel and the hardness of the abrasive are two different concepts. The same abrasive can be made into grinding wheels with different hardness, which mainly depends on the properties and quantity of the bonding agent and the manufacturing process of the grinding wheel. The significant difference between grinding and cutting is that the grinding wheel has "self-sharpness". When you choose the hardness of the grinding wheel, you are actually choosing the self-sharpness of the grinding wheel. I hope that the sharp abrasive particles do not fall off too early, and do not blunt and not fall off.
The general principle for selecting the hardness of the grinding wheel is: When processing soft metals, in order to prevent the abrasive from falling off prematurely, a hard grinding wheel is selected. When processing hard metals, in order to make the dull abrasive particles fall off in time, so that new abrasive particles with sharp edges and corners (ie, self-sharpening) are exposed, a soft grinding wheel is selected. The former is because when grinding soft materials, the abrasive wear of the grinding wheel is very slow and does not need to be detached too early; the latter is because when grinding hard materials, the abrasive wear of the grinding wheel is faster and requires faster Update.
When fine grinding, in order to ensure the grinding accuracy and roughness, a slightly harder grinding wheel should be used. The workpiece material has poor thermal conductivity and is prone to burns and cracks (such as grinding cemented carbide), so the selected grinding wheel should be softer.
We are grinding wheel exporters. If you have any questions about grinding wheels, we are happy to answer them.
没有评论:
发表评论